Internal Corrosion within Water Distribution Systems
Corrosion is natures way of returning certain processed metals such as iron, steel, and copper to their native states as chemical compounds or minerals. For example, iron in its natural state becomes an oxidized compound (i.e., Fe2O3, FeO, Fe3O4), but when processed into iron and steel pipe, it loses oxygen and becomes elemental iron (FeO). In the presence of water and oxygen, nature relentlessly attacks this steel, reverting the elemental iron (FeO) back to its natural oxidized state.
Translate this page
Microsoft® Translator
The Corrosion Electrochemical Cell:
Although corrosion is a complicated process, it can be most easily explained as an electrochemical reaction involving three steps as listed below: While reviewing this illustration, keep in mind that SPER Chemical produces corrosion inhibitor formulations such as Protect-All, Sequest-All, and Linear2 that include both anodic and cathodic inhibitor ingredients. These ingredients can effectively “deaden” these reactive sites while creating a protective coating on interior pipe surfaces continuously interfering with the electrical circuit required to initiate the corrosion process.
1. Metallic loss occurs from that part of the internal metal pipe called the “anodic area” (anode). In this case, iron (Fe0) is lost to the water solution and becomes oxidized to Fe++ ion.
2. As a result of the formation of Fe++, two electrons are released to flow through the steel to the cathodic area (cathode).
3. Oxygen (O2) in the water solution moves to the cathode to form hydroxyl ions (OH-) at the surface of the metal. In the absence of oxygen, hydrogen ion (H+) participates in the reaction at the cathode instead of oxygen.
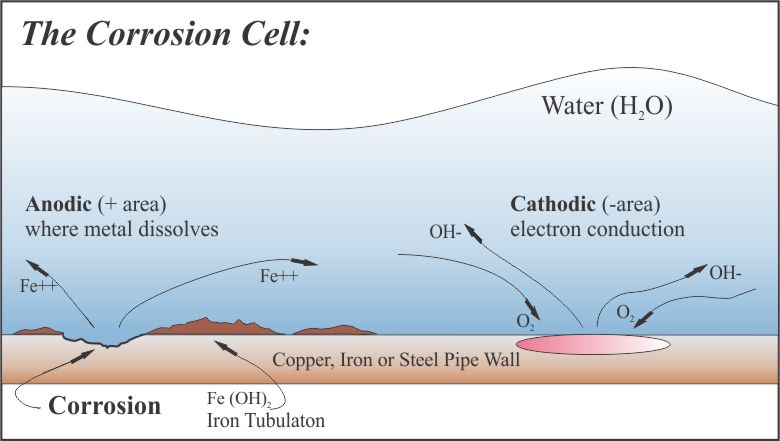
Every metal surface is covered with inumerable small anodes and cathodes as shown above. These sites usually develop from: (A) surface irregularities from manufacturing; (B) stresses from welding and forming; and/or (C) metallic composition differences of at the pipe surface. As noted above, there are three basic steps necessary for corrosion to proceed electrochemically.
Types of Corrosion:
Uniform Corrosion:
When uniform corrosion of metal pipe occurs, it can be typically due to an adaptation creating a polyelectrode at the surface of the pipe. This refers to the electrochemical reaction whereby any one particular site on the metal surface can become anodic one instant and cathodic the next. Because anodic sites shift or creep about the surface, the rate of loss of metal is relatively uniform over the metal surface.
Again, SPER Chemical Corporation produces corrosion inhibitor water treatment formulation that contain both anodic and cathodic inhibitor ingredients to prevent this electrochemical reaction while coating the interior surface of the pipe wall thereby effectively diminishing corrosion rates and putting a barrier between the water and the pipe surface.
Galvanic Corrosion:
If the piping system consists of different metals, or are adjacent to distinct metals, the cathodic and anodic areas are fixed and so-called galvanic corrosion can occur. Galvanic corrosion results when two different types of metals or alloys contact each other, and the elements of the corrosion cell are present. One of the metals serves as the anode, and thus deteriorates, while the other serves as the cathode.
Galvanic Series refers to the arrangement of the metal alloys in order of their tendencies to be anodic. If any two of the metals from different groups in this arrangement are connected in an aqueous environment, the metal that tends to be most anodic will be allowing the second metal to be cathodic. In general, the farther apart these metals are in the Galvanic Series the greater the potential is for corrosion to occur.
SPER Chemical Corporation produces corrosion inhibitor water treatment formulations that contain both anodic and cathodic inhibitor ingredients. Our formulations will help to prevent this electrochemical reaction while also creating a protective coating on the interior surface of the pipe wall maintaining a barrier between the water and pipe surface therby effectively diminishing corrosion rates.
NOTICE:
The information herein is to our knowledge true and accurate. All information appearing on this document is based on data obtained from the manufacturer and/or recognized technical sources. Because of conditions beyond our control, we make no warranty or representation, expressed or implied, except that the product discussed herein conform to the chemical descriptions shown on their labels/product data Information is supplied upon the condition that the persons receiving same will make their own determination as to its suitability for their purposes prior to use. In no event will SPER Chemical Corporation be responsible for damages of any nature whatsoever resulting from the use of or reliance upon information or the product to which the information refers. No agent, representative or employee of this company is authorized to vary any of the terms of this notice